Customizing Dental Restorations with 3D Printing
Customizing Dental Restorations with 3D Printing
Blog Article
The world of dental care has experienced an innovative transformation over the last couple of decades, with dental CAD/CAM (computer-aided design/computer-aided manufacturing) innovation at the forefront of this advancement. This state-of-the-art development utilizes sophisticated software program and exact machinery to style and manufacture dental restorations, such as crowns, bridges, inlays, veneers, and onlays. Dental CAD/CAM milling burs are an essential element in this process, playing a vital role in forming complex dental reconstructions with exceptional precision.
Milling burs are cutting devices utilized together with dental milling makers to take and complete dental prosthetics from various products. These tools must be sharp and exceptionally resilient, given the accuracy required and the solidity of materials they usually collaborate with. Regular materials consist of resins, steels, and ceramics, although progressively, zirconia has actually become the product of option for several dental repairs due to its remarkable strength, biocompatibility, and visual potential.
Dental zirconia spaces, sometimes described as zirconia discs or blocks, are pre-manufactured forms of zirconia used in the milling procedure. Zirconia, a crystalline form of zirconium dioxide (ZrO2), attracts attention for its mechanical homes, which approach those of metals. These buildings include high fracture sturdiness, resistance to use, and a shade that closely simulates all-natural teeth, making it perfect for dental applications. The manufacturing of dental zirconia starts with the formation of these spaces. They are fabricated under high pressure and temperature level problems, which impart remarkable density and mechanical qualities.
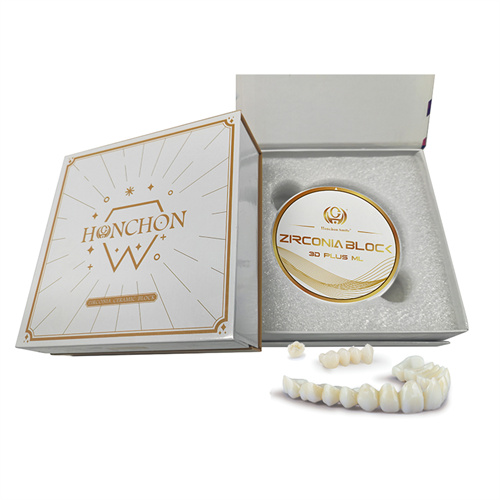
Check out the current improvements in dental CAD/CAM innovation, zirconia milling, and 5-axis dental milling machines that are changing restorative dentistry. Discover how technologies like 3D plus Multiayer Blocks are improving precision, person, and performance contentment in contemporary dental treatment.
As soon as the zirconia blanks are created, they need to be sintered, commonly in a zirconia sintering furnace. The sintering process is critical, as it maintains the zirconia structure and locks in its biocompatible and visual top qualities.
Advanced milling makers, particularly 5-axis dental milling makers, have actually transformed the manufacturing of dental restorations. Commonly, dental remediations required labor-intensive procedures and a considerable quantity of time to produce. The advancement to 5-axis innovation has actually changed this dramatically. Unlike 3-axis makers, which relocate three direct axes (Y, x, and z), 5-axis equipments add 2 additional rotational axes (A and B). This provides the milling machine the adaptability to approach the zirconia blank from any type of angle, which is seriously important for producing complex forms and damages precisely and efficiently. The result is precision-crafted reconstructions that fit much better, really feel much more comfy, and look even more natural.
These innovative materials combine the benefits of multi-layered zirconia with the precision of 3D printing technology. The multi-layered aspect refers to the gradient in color and translucency within the zirconia block, mimicking the natural transition from dentin to enamel found in real teeth.
3D printing technology has included an additional layer of modification and accuracy to this approach. By integrating CAD/CAM designs with 3D printing, the elaborate details of the dental restoration can be captured and printed layer by layer. This causes also higher accuracy in fit and aesthetic appeals, which is critical for client complete satisfaction.
The combination of dental CAD/CAM systems, high-quality milling burs, dental zirconia spaces, sophisticated sintering heaters, 5-axis milling makers, and the newest development in 3D plus Multilayer Blocks exemplifies the future of dental prosthetics. These modern technologies not only guarantee accuracy and integrity however also streamline the production procedure, making it quicker and much more cost-efficient. The surge impact of these advancements extends much beyond research laboratories and makers. Dental experts can supply better solution with quicker turn-around times, while patients profit from even more resilient, better-fitting, and aesthetically pleasing reconstructions. The shift from traditional approaches to electronic workflows in dental techniques highlights the relocation towards boosting precision, efficiency, and total individual experience.
The precision afforded by these modern technologies means prosthetics can be made and fabricated with a high level of precision, decreasing the demand for repeated installations or changes. This degree of precision is largely driven by the quality of dental CAD/CAM systems and the use of premium milling burs with the ability of great detailing. The handling of dental zirconia blanks in zirconia sintering heating systems makes certain that the final item meets the greatest criteria of resilience and biocompatibility.
The development of 5-axis dental milling machines has broadened the extent of what is possible in corrective dentistry. These makers can mill facility geometries and fine details which were not feasible prior to, leading the way for extra sophisticated dental options. This technical jump has additionally made it possible to take advantage of 3D plus Multilayer Blocks effectively. These multilayer blocks supply natural-looking reconstructions that duplicate the rank of color and translucency found in genuine teeth.
Furthermore, the continual development in zirconia materials and CAD/CAM modern technologies perpetuates a much more reliable and efficient dental treatment setting. Dental professionals can currently accomplish even more predictable outcomes, reducing chair time and enhancing client fulfillment. The thorough integration of these innovations right into regular dental method represents a seismic change from responsive to positive dental treatment, where electronic impressions, specific milling, and prompt adjustments become standard method.
An additional essential aspect is the environmental and economic benefits these innovations bring. By minimizing product waste and maximizing using resources, dental techniques can run a lot more sustainably. The performance gains likewise equate right into price financial savings that can be passed on to patients, making high-quality dental treatment more available. The worldwide integration of these innovative products and machines into dental curricula ensures that future dental experts are skilled in the most recent technological advances, cultivating a society of constant improvement and advancement.
In recap, the harmony between dental CAD/CAM systems, durable milling burs, high-quality zirconia blanks, efficient zirconia sintering furnaces, advanced 5-axis dental milling makers, and cutting edge 3D plus Multilayer Blocks is driving a new era in dentistry. This combination is transforming how dental restorations are designed, made, and implemented, bring about far better end results for both dentists and patients. As innovation proceeds to develop, the future holds much more assurance for improvements that will better transform dental treatment, making it a lot more exact, reliable, and patient-friendly than ever. Report this page